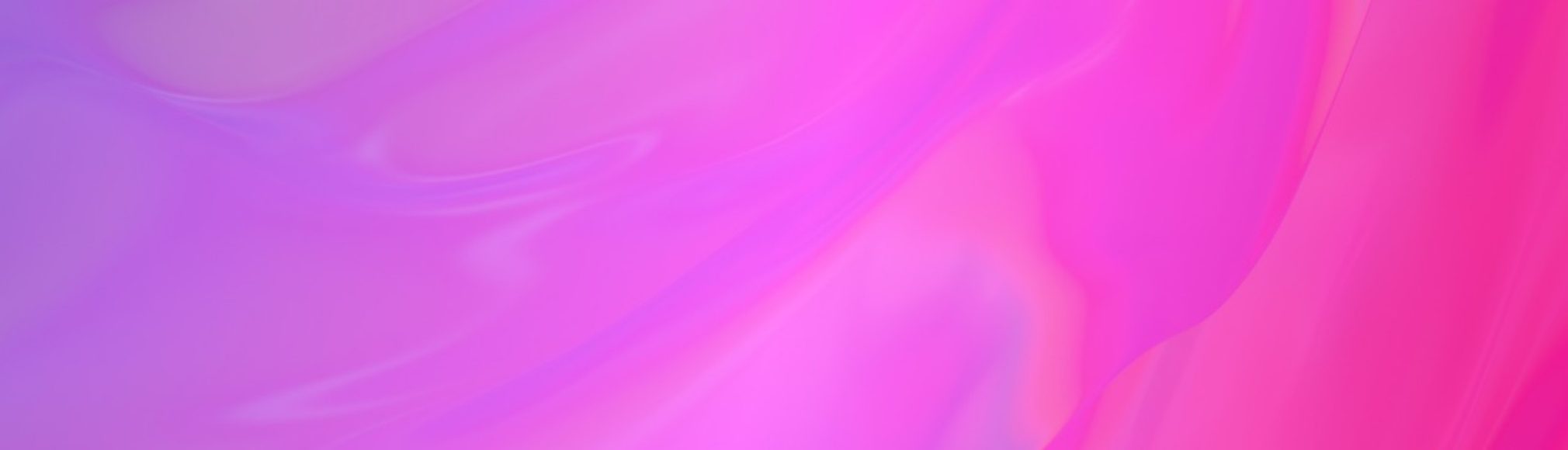
11 June 2020
Making Personal Protective Equipment (PPE) for frontline workers requires skills and expertise that Nelipak Healthcare Packaging has been perfecting for years, but the company didn’t know it until the pandemic struck. Lyndsey McMillan, Senior Director of R&D, takes up the story.
As a global provider of specialist healthcare packaging to the life sciences industry, we are used to operating at the leading edge but the extraordinary circumstances around Covid-19 prompted a whole new kind of product development. Like any company involved in healthcare, Nelipak wanted to play a part when the pandemic struck, and we soon found ourselves involved in the race to supply PPE.
As part of Ireland’s healthcare cluster, we have close relationships with companies in the same ecosystem, so it’s not that surprising that we found a role manufacturing equipment to help combat the pandemic. One was a face shield, part of the essential PPE that frontline healthcare workers are desperately short of, the other a sanitation wipe to mop Covid-19 from the skin. Both products are now in production in our Irish facilities.
Live prototyping over video.
When another Irish company came looking to mass produce a face shield we knew we had the tools and facilities to get the job done. Culturally, we have always seen ourselves as entrepreneurial with a ‘we can do it’ attitude. What we also have is industrial designer and engineers to design something from scratch and to quickly develop the production lines to make them.
There is huge demand among healthcare workers for clear plastic shields that cover the entire face, and lot of designs from people for making them with 3D printers. The problem is that they weren’t able to get them out fast enough. Not only are we expert in thermoforming, heating plastic to form a shape in a mould that can be trimmed and fitted to become face shields, we have access to the raw materials and machines to manufacture at scale.
As result of the pandemic, we were seeing a drop-off in some of our other lines – such as elective surgery products because of fewer operations – so we had some spare capacity. The challenge was coming up with a design that was ‘manufacturing ready’ and comfortable enough to wear for long periods of time.
One of our designers, Alan Kelly, was working with a combination of 3D printing, laser cutting and CAD (Computer Aided Design) in our innovation centre. The traditional approach would be to draft a design, email it to the client, and go back and forward making iterative changes. But time was a luxury we didn’t have, so he was prototyping by video over Teams and WhatsApp, literally doing the design live with the customer watching.
We were making prototypes in batches of 10-20 and delivered over 50 iterations in around two weeks, each one going out to customers and healthcare users who gave us their feedback. It was a fast turnaround that we had experimented with in the past, not realising we were practising for an event that we couldn’t have imagined.
Meeting strict specifications and controls.
We are also making a sanitation wipe for cleaning Covid-19 from the skin. A National University of Galway start-up, Aquila Bioscience, had come up with a ground-breaking anti-bioagent wipe for frontline services that turned out to be effective on coronaviruses. It’s not a disinfectant, so it won’t hurt skin or eyes or cause any irritation, which makes it ideal for frontline workers – ambulance, postal and police as well as healthcare.
Before we got involved and scaled the process, the wipes were packed in labs by student volunteers. Now, Aquila provides the fluid and we assemble all the other components and manage the supply chain. We ‘syringe in’ a certain volume of their liquid to wet the wipes, seal, label and put them in cartons. It was not as big a pivot as the shield, because they are made in our Clara facility where we specialise in kits for different medical devices.
Like every company now functioning as an essential business, we have to protect employees who can’t work from home and have imposed strict social distancing in our plants and canteens, and segregated shifts so there is no overlap. We’ve been lucky, with only a small fraction of our 1,400 global workforce catching the virus.
So far, we have made over 400,000 face shields in Galway that are being used across Europe. We have also been collaborating with our US operations who like us, are mass-producing a number of face shield designs. We are ramping up production of wipes. Packing them is a manual process at the moment, but we plan to automate and scale further.
One of the lessons we’ve all learned from this crisis is the value of having expertise in your home country rather than having to rely on unknown overseas suppliers for essential PPE. While we never could have predicted the part we now play in the pandemic, our in-house design skills and ability to manufacture to strict specifications, standards and controls have enabled us to rise to the challenge and produce high quality products that can hopefully make a difference.